Oxford MEStar approached us to design and manufacture an integrated handling and vision inspection system to quality check and sort specially packaged ‘corneal scaffolds’.
Oxford MEStar Limited, established by Professor Zhanfeng Cui, FREng., is a young spin-out company from the Institute of Biomedical Engineering of Oxford University devoting themselves to developing bioengineering solutions and technology transfer between the UK and China.
The project objective was to develop new processing technologies for the growing regenerative healthcare markets around the world.
The science
The technique is to improve development of enabling technologies for tissue engineering and stem cell therapy. The process analyses the visual property of each cornea following the manufacturing process, each part being a closely guarded secret.
The objective for the scientists was to semi-automate the inspection process as part of an in-line production process to increase throughput. This involved mechanical positioning, motion control system, a vision inspection system and a laser analysis unit, all to be integrated and work as one.
The initial difficulty was to detect the cornea. With the overall package measuring 80 mm x 100 mm, a transparent cornea, in a transparent scaffold, in a transparent package, the challenge was clear!
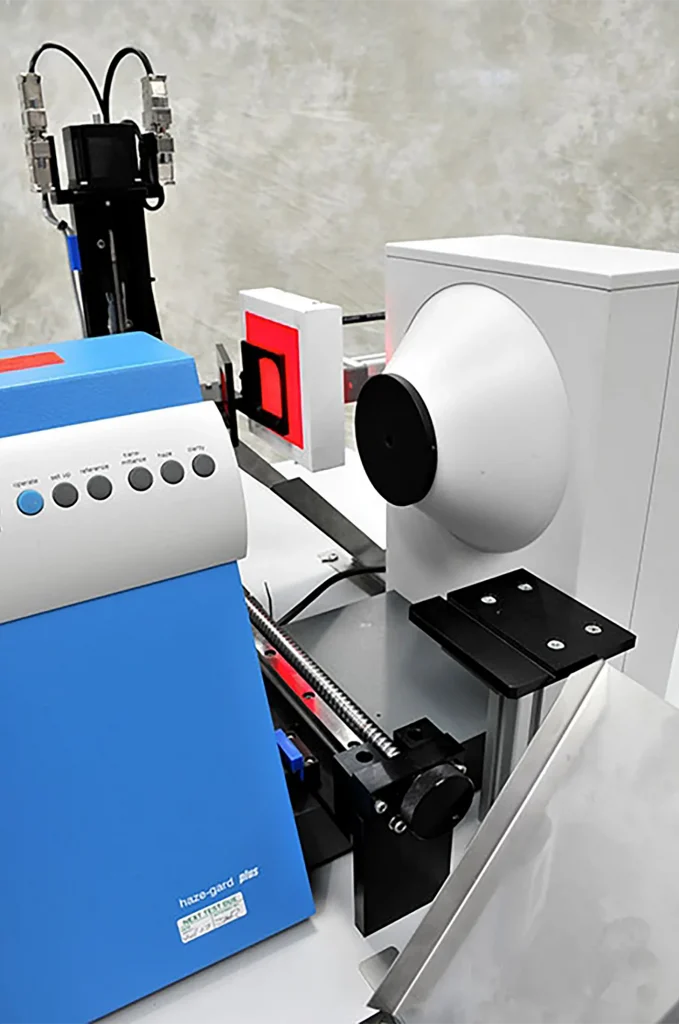
The engineered solution
The basic machine requirement called for the vision system and laser analysis unit to be integrated with a two-axis linear positioning system and PC motion control software that included a Human-Machine Interface (HMI) screen prompts and status information.
The near transparent items are suspended in a ‘petridish’ solution, making it difficult to determine their exact position with relation to the packaging. To resolve this initial challenge, we worked with imaging specialist Scorpion Vision to develop a suitable camera vision system. The end solution was able to evaluate the appearance and location of the corneal scaffold to within 0.1 mm.
The system is mounted on a machine frame built with the MiniTec aluminium profile system and consists of a bespoke XZ Motorised slide assembly with motion controller, vision system, laser analysis unit and control computers.
The motion mechanics – custom stepper driven ball screw positioning stages with single linear motion guide bearings – are designed specifically for the application to maximise the space on the work platform. With a 500 mm x 50 mm travel range, the stages include manual drive wheels to allow the operator to position the axes under power-off conditions to maintain the machine. The motion controller, Arcus Technology PMX-4, is an advanced micro-stepping unit with fast synchronising inputs and outputs for the coordination of motion and external events required for the application.
To improve the consistency of tests and ease of use for multiple operators, we also provided a Graphical User Interface (GUI) front-end program that allowed simple system operation without the need to program. The HMI touch-screen displays the machine phases – loading the package, automatically locating the cornea and its scaffold, the laser inspection phase and pass or fail for acceptance or rejection – then prompts the technician to load another package. Move parameters, speeds, time delays and other adjustment features are included along with the display of status information such as system state, axis position, I/O condition, axis and drive faults.
Overview
- An operator manually feeds the packages into the machine and the semi-automatic operation presents them to the vision system which then locates the scaffold position within 0.1 mm.
- The data from the vision system is used to re-position the scaffold to an optimal location within the full view of the laser analysis system used to determine the condition of the cornea from its optical properties.
- Finally, the package is accepted or rejected and transferred into pass or fail chutes for further processing.
The design, production and quality inspection all took place at our Basingstoke plant and the stages were designed, manufactured and built in-house along with the gripper mechanism, brackets and the fixtures for locating the imaging and laser inspection sub-systems.
The result
We were selected based on successful experience within the regenerative bioengineering sector and the completeness of service that enabled a quick delivery of an integrated solution.
As with many development processes, flexibility was a key factor in system design. The mechanical assembly is modular and the Arcus controller offers easy and straightforward programming. This programming flexibility allows Oxford MEStar to adapt the system as the research project progresses, including the ability to add encoder feedback for position verification should they wish to increase the system repeatability in the future.
We worked closely with the scientific team of Oxford MEStar during all phases of this successful project and delivered the complete integrated Inspection System within a very tight timeframe.
The machine is now in operation at a production and research facility in China, where it is helping to develop and improve the quality of the cornea inspection process.
If you are looking for a dedicated partner to work alongside for your electro-mechanical motion project, get in touch.
We’ll work with you to develop the best solution for your specific challenge, no matter how complicated.
Arrange a visit and meet the team: